In the first part of this deep dive into ballistic protection, we talked about body armor. What about protecting your dome? Let’s take a brief look back at the history of helmets to better understand their value.
The first documented use of helmets in combat was found in ancient Sumeria and Akkadian civilization, both from the region we would call Mesopotamia, circa 2300 BCE. The earliest bronze helmets are reported to have come from the Mycenae in 1700 BCE, and these Greeks were also believed to be the inventors of the first plate armor set.
Use of combat helmets was prolific within the Ancient Greek and Roman Empires, at first being made of leather and eventually various types of metal and metal-alloys — initially leather and brass, then bronze and iron. As weaponry became more sophisticated, so too did the need for more robust protections of soldier’s heads. Military use of helmets was initially employed to prevent the wearer from cuts, arrows, and low-velocity musketry.
Eventually, in the 17th century, the use of military helmets declined as rifled firearms entered the battlefield. While some holdouts, like Napoleonic era cavalry, still wore ornate helmets, they served more as status symbols than protection from ballistic threats. However, in the early 20th century at the start of World War I, the widespread use of battlefield artillery resurrected the need for helmets — steel ones. Modern battlefield hazards included lateral frag from artillery and falling debris, as well as bullets (the latter would not be defeated until much later in the late 20th and early 21st century).
After steel, modern battlefield soldiers wore PASGT (Personnel Armor System for Ground Troops) and similar helmets crafted from Kevlar, Aramid, or a similar synthetic fiber. More recently, they are crafted from ultra-high-density polyethylene. The lightweight yet ultra-strong materials protect against lateral frag and shrapnel, many pistol rounds, and even rifle rounds, as we will discuss in this article.
Another major adaptation has been protection from non-ballistic threats, like a concussive shockwave, as well as the internal padding. Sufficient padding inside a helmet helps absorb the inertia from ballistic threats and mitigate backface deformation (more on this later), as well as making the helmet more comfortable to wear.
Above: The Crye Precision AirFrame uses a unique two-piece overlapping shell that offers improved ventilation. Crye says it can also “reduce the damaging effects of explosive blast waves.”
Helmets vs. Body Armor: How Are They Different?
Both stop bullets and shrapnel, but there are some inherent differences. While some body armor may be curved, it has nowhere near the curvature of a helmet, which essentially needs to be a partial sphere. This creates challenges with any ballistic material and is where the art and science of ballistic protection meet. In order to have a robust armor system on your head, there needs to be consistency in the layers and density throughout the armor system so as not to have any failure points.
“If you want a quarter-inch helmet, it needs to be a quarter-inch all the way around. With the fabrication process, without crown-reinforcements the thickness of your helmet will vary from crown [of the head] to sides. We add crown reinforcements to help prevent that,” Dub Robertson, retired Master Sgt. (USMC), Plant Manager for Hard Head Veterans, elaborated.
This is a delicate balance, Robertson said, in that if you add more plies (additional layers) or you don’t pay attention to this balance, you can get cosmetic deformations like wrinkles and bubbles, which may or may not lead to a ballistic failure. Specifically, he said you want the inside of the helmet to be as smooth as possible. This is why helmets that defeat ballistic threats are much harder to fabricate than non-ballistic helmets.
Director of Research & Development of Engineering at HighCom Ed Clark explained their proprietary helmet fabrication process: “The technology we utilize is the XTclave, which is our proprietary technology. It’s a different method of consolidating the materials together to create the helmet. As you probably are aware, when these raw materials come in, they’re on a roll and they’re relatively flexible. They’re effectively like a big sheet of fabric. We then put those fabrics onto a ply-cutting machine to form the desired shapes, then stack multiple layers of material on top of one another.
This material stack is then put into a pre-forming press to give it an initial shape. Then, we do a final consolidation stage through our XTclave, which imparts the full consolidation pressure and temperature into the shell. Traditionally, most manufacturers will utilize only a press, so in effect they’re applying the consolidation pressure only through one plane.”
What’s more, the ultra-high-molecular-weight polyethylene (UHMWPE), colloquially known as poly, doesn’t paint well. Unlike armor, helmets are often worn outside of a carrier and are exposed to the elements, so the exterior finish is an important consideration. This is where “skins” come in.
“Typically, skins are an aramid material, aka Kevlar. [Hard Head Veterans] typically do one skin inner layer, and one skin outer layer. Obviously, using aramid helps with the ballistic properties of the helmet. We do know some companies out there are using carbon fiber; they do the ‘guts’ of the helmet in [UHMW]PE, but their first or second skin is carbon fiber. We’ve seen some videos of them shooting a helmet with this type of a configuration, and while there is no dent in the helmet, since it helps with compression, there is no ballistic protection offered from carbon fiber.
It helps with blunt impact, due to the lack of compression in the material, but has no ballistic protection advantages, so we haven’t used it in our helmets,” Robertson from Hard Head Veterans explained on a call. Also, carbon fiber is pretty expensive, which adds to the cost of the helmet.
Helmets are about as extreme of a curve as you’re going to get and are not as straightforward as something like pressing body armor — even curved plates. Fabrication processes like the proprietary XTclave use a fluid medium to transfer pressure, which works well when creating things with compound curves and complex geometries. However, other standard methods of fabrication, such as layering plies of UHMWPE, are still strong. As long as the manufacturer understands the dynamics of crown reinforcement and it passes ballistic testing, you should be good to go.
Testing Protocols for Helmets
Ballistic helmets go through a similar testing protocol to body armor, with some slight nuanced differences. Most of the helmets on the market are only rated to defeat pistol rounds, which technically is a Level II or IIA rating. Per NIJ 0106.01 for ballistic helmets, to obtain a Type II rating, the helmet must defeat high-velocity pistol-caliber rounds such as the .357 Magnum or high-velocity 9mm (+P or +P+).
One company who I interviewed for this piece manufactures a rifle rated helmet — HighCom Security’s RCH helmet. The RCH is rated against common rifle threats and boasts a Level III rating, able to defeat 7.26×39, 5.56×45 XM193, and even the hard-hitting 7.62×51 NATO.
Another consideration when it comes to ballistic helmets is protection from shrapnel, often referred to as lateral frag. The benchmark for this is MIL-STD-662F, and this tests against different weights of shrapnel that one would see on the battlefield or in an area of operation, going from 2 grains to 44 grains in weight, at varying velocities.
The MIL-STD-662F framework is utilized to grade armor — that includes body armor, armored seats for aircraft and ground vehicles, crew station armor on military vessels, aircraft armor, bulkheads, tactical shelters, and even “clear armor” like windshields, shields, or windows. The RCH abides by the MIL-STD-662F in addition to NIJ 0101.06 Level III Rating.
Considering the extreme curvature of a helmet, the NIJ’s testing is incredibly in-depth, and requires different hit angles to pass — basic plane, coronal plane, sagittal plane, and also takes into account the angle of attack when testing. There’s an NIJ standard for Ballistic Helmets published if you want to go deep on the specs, but refer to the table for an excerpt.
Above: Hard Head Veterans (HHV) newest ATE Lite helmets are made in Sweetwater, Texas, using a combination of UHMWPE and aramid fibers.
What About Backface Deformation?
As with body armor, backface deformation is top of mind for ballistic helmets as well. While there’s more “padding” with a helmet — both the structural “impact layer” and the softer padding that’s used for comfort — backface deformation is a non-trivial consideration with ballistic helmets. This started from a research and development paper from the U.S. Army where 25mm was the standard, but many companies today have gotten down to 15mm at max, and in some cases 8mm or less with high-velocity pistol rounds, well below the U.S. Government standards.
Per HHV’s spec sheet on their HPE helmet, which I had the chance to test, the backface deformation of a 9mm 124-grain round screaming at over 1,400 feet per second — far above most factory loads — is at max 15mm on the crown, and only 8mm at the back of the head.
This deformation is typically not seen unless you peel off the protective padding of the helmet post-gunshot anyway, but it’s comforting (as comfortable as you can get with getting shot in the head) to know that the structure of the helmet will deform only about ⅓ of an inch.
“Sometimes, we get helmets back for a size exchange, and we notice the impact pads are out of there. The impact pads are there for a reason! They’re specifically designed to reduce backface deformation. The comfort pads aren’t even involved in the testing, we just send the helmet and the impact pads,” Robertson stated.
Helmet Weight: It Matters!
Considering the human head itself weighs about 8 pounds, and every inch you move your head forward from vertical alignment functionally adds 10 pounds to your dome, any ballistic helmet you put on your head will need to be lightweight in order for you to be combat or mission effective. This is just as important, if not more important than body armor being lightweight. Helmet weight has been proven in studies to affect cognitive performance. When in a hostile engagement, your most valuable weapon is not your rifle or sidearm, but your brain; helmet weight and cognitive fatigue are correlated.
Moreover, even the strain that is placed on your neck affects cognitive performance. There are also muscular considerations as multiple studies have found that the heavier the helmet, the more muscular fatigue and/or risk of injury while operating in the field.
“There is a big drive toward lightweight protection recently, and it is becoming more and more apparent with a lot of armed forces … As forces are becoming more advanced, they’re using more equipment to assist — headsets, NVGs, augmented reality. All that equipment is adding weight. And if it’s going on the head, it’s putting more load on the head, which means your endurance isn’t going to be as long as you’d like, and you might suffer neck trauma down the line.
So, taking what we term ‘dead weight’ out of a helmet shell is a benefit because it means you can either put more gear back onto your operator’s head, or you’re allowing them to wear it for longer,” Clark of HighCom explained, underscoring the importance and validity of the previously mentioned studies.
Above: Oregon Ballistic Laboratories (OBL) also tests helmets according to NIJ standards. Each helmet is tested from a variety of angles.
So … What Helmet Should You Buy?
Just like with body armor, the helmet that’s right for you is the one that fits your needs and budget. If you don’t need ballistic protection, an unarmored “bump helmet” provides basic impact protection and the ability to wear head-mounted accessories like night vision. If you’re not operating where you can expect to see rifle fire and lateral frag, or just want a layer of protection for your most valuable weapon (your brain), a pistol-rated NIJ Level II helmet may be perfect for you, and will only run you a few hundred dollars.
If you want something that can stop incoming fire from an AK and only weigh a couple of pounds, you’re in luck — they make those now. Just be realistic about the threats you’re likely to face and remember that higher levels of protection always come with at least a few minor trade-offs.
Read More
Subscribe to Recoil Offgrid’s free newsletter for more content like this.
Editor’s Note: This article has been modified from its original print version for the web.
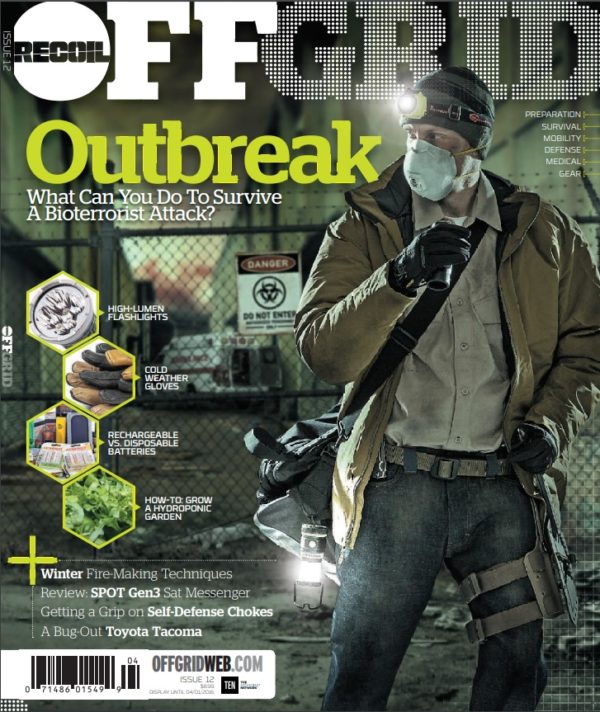
Subscribe Today and Save!
STAY SAFE: Download a Free copy of the OFFGRID Outbreak Issue
In issue 12, Offgrid Magazine took a hard look at what you should be aware of in the event of a viral outbreak. We’re now offering a free digital copy of the OffGrid Outbreak issue when you subscribe to the OffGrid email newsletter. Sign up and get your free digital copy